PRODUCT
Contact Us
Phone: +86-0539-8228838
Wechat: 18253974567
Whatsapp: +8618253974567
E-mail: jack@jlfmcl.com
Address : Luozhuang district.Linyicity Shandong Province,China
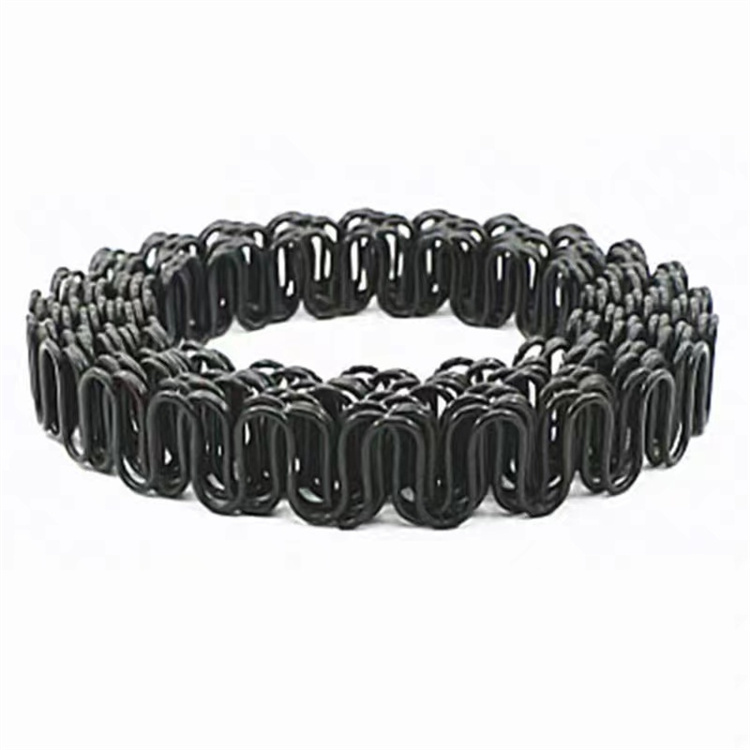
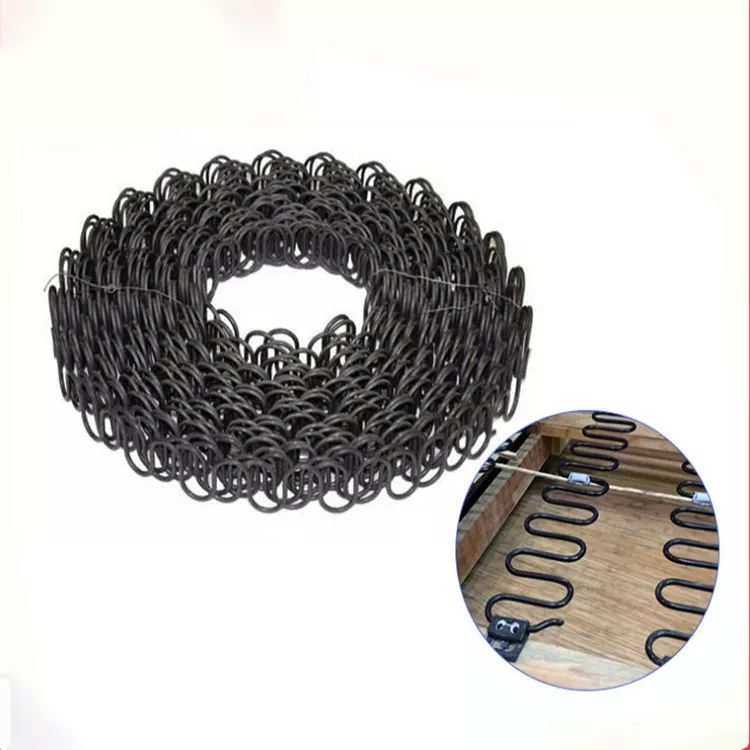
Zigzag spring
Classification:
keyword:
Zigzag spring
Whatsapp:
E-mail:
Message
DESCRIPTION
Roll zigzag spring is an import part of the sofa structure, also know as S spring tension spring, because the shape of the letter S has tensile properties. The snake spring is fixed on the sofa with the snake spring buckle. It has the functions of good elasticity and long using life. The camber of seat cushion can be adjusted as well.
Carefully selected ingredients
Featured material manufacturing, high arch position, short spacing, enough material.
Exquisite workmanship
Machine one-time forming back bend, neat cutting , and not easy to scratch when install.
Speical craft
Anti-rust electrophoretic treatment, anti-oxidation, not easy to rust.
Factory direct sales
Factory direct sales, strong supply capacity, OEM is acceptabled.
Product parameters
Item
|
Value
|
Place of Origin
|
China
|
Brand Name
|
Jianli
|
Model Number
|
2.6mm-4.3mm
|
Style
|
Curve Zigzag Spring
|
Material
|
Steel
|
Usage
|
Furniture
|
Type
|
Curve Zigzag Spring
|
Packing
|
Woven bag winding
|
Use
|
Home Furniture
|
Packing Process
|
Customized
|
Color
|
Black/White
|
Wire diameter
|
2.6~4.3mm
|
Size
|
Customized Size
|
OEM
|
Acceptable
|
Rolling Zigzag Spring | |||||
H(mm) | W(mm) | S(cm) | D(mm) | L(mm) | R |
43-51 | 16-35 | 8-15 | 2.6-4.3 | Cient Requirement | - |
Round Zigzag Spring | |||||
H(mm) | W(mm) | S(cm) | D(mm) | L(mm) | R |
43-51 | 16-35 | 25-50 | 2.6-4.3 | Cient Requirement | - |
Functional Zigzag Spring | |||||
H(mm) | W(mm) | S(cm) | D(mm) | L(mm) | R |
43-51 | 16-35 | 25-50 | 2.6-4.3 | Cient Requirement | 45-120 |
Flat Zigzag Spring | |||||
H(mm) | W(mm) | S(cm) | D(mm) | L(mm) | R |
43-51 | 16-35 | - | 2.6-4.3 | Cient Requirement | - |
Curve Zigzag Spring | |||||
H(mm) | W(mm) | S(cm) | D(mm) | L(mm) | R |
43-51 | 16-35 | 3.25 | 2.6-4.3 | Cient Requirement | - |
Super Loop Zigzag Spring | |||||
H(mm) | W(mm) | S(cm) | D(mm) | L(mm) | R |
70-76 | 30.50 | 5-50 | 2.6-4.3 | Cient Requirement | - |
Application scenarios
Packaging display
GLOBAL COOPERATION
Customer photos
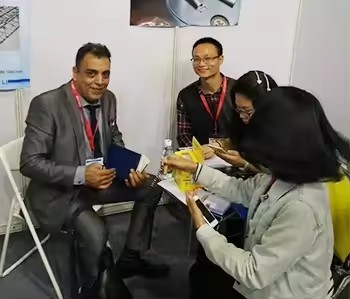
Customer photos
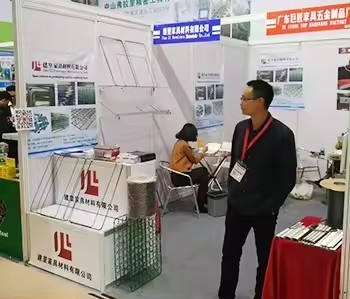
Customer photos
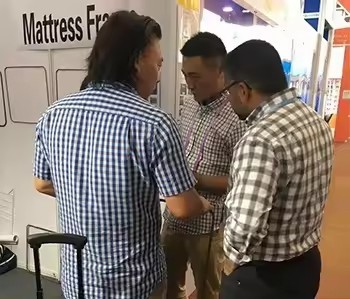
Customer photos
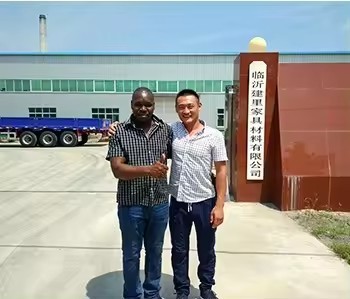
CERTIFICATE
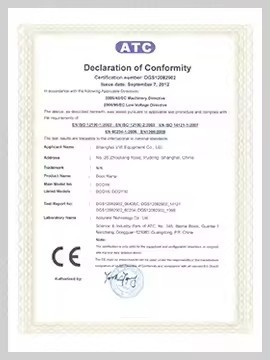
Honor
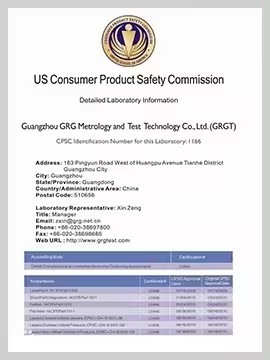
Honor
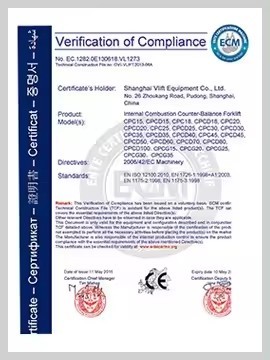
Honor
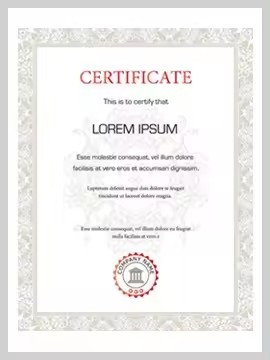
Honor
RELATED PRODUCTS
FAQ
What are the commonly used production methods for various spring steel wires?
(Steel) Wire rod - Surface treatment - Drawing (This method can be used for mattress steel wire)
How to treat the surface of spring steel wire?
Generally, acid pickling and phosphating are used to remove iron oxide scale and form a phosphating film; There are also a few who use mechanical methods for processing. The purpose is to meet the requirements of the cold drawing process and obtain a smooth surface. For spring steel wires that require high fatigue life, such as valve spring steel wires, the coil should be peeled to reduce surface defects. If the steel plant can grind the steel billet, it is also beneficial to reduce defects.
How to wire draw the spring steel wire?
The drawing process of finished products has a significant impact on product performance. Generally, a larger total reduction rate of about 90% (see area reduction rate) and a smaller pass reduction rate (about 10% -20%) are used to ensure the toughness of the product. For high-strength spring steel wire, the outlet temperature of each pass of steel wire should be controlled below 150 ℃ during drawing to prevent torsion cracks caused by strain aging, which is the main defect causing steel wire scrap. Therefore, good lubrication and sufficient cooling are necessary during drawing, and using smaller pass reduction rates and drawing speeds can help reduce the temperature rise of the steel wire.
Production process of spring steel wire for beds
1. When selecting raw materials, consideration should be given to their tensile strength and torsional performance, and torsional tests should be conducted to ensure that the raw materials do not crack and the surface is flat. 2. During heat treatment, decarburization of the raw materials should be avoided to ensure a high carbon content and obtain a more stable sorbite structure. 3. When drawing semi-finished products, a process with high compression rate, multiple passes, and a small portion of compression rate should be adopted, as well as a reasonable drawing route. During the drawing process, the drawing equipment, lubrication and cooling conditions, and mold dimensions must be strictly followed according to the standards to ensure the flatness of the finished product. 4. Develop a reasonable immersion temperature to ensure that the product is time sensitive.